Major Systems Engineering & Test Projects
This is a subset of many scores of projects over 35 years.
Follow the "Click Here" if you want to dig-in to the detailed challenges and my responses on these projects.
Uber ATG | Systems Directorate
Stand-Up Systems Engineering for Self Driving Vehicles
Uber's Advanced Technology Group (ATG) experienced a fatal accident in Tempe, Arizona in March of 2018. One of the outcomes of the investigation was the need for a strong Systems Engineering capability.
​
Nearly two years later, three attempts to stand up a proper Systems Engineering Directorate had failed.
My first assignment as Director of Systems Engineering & Tooling was to build out our Systems Engineering capacity and increase the flow of formally managed requirements to the Autonomy team.
​
By the time I moved to my next assignment five months later, we had ingested over 10,000 requirements and were continuing to refine and generate more.
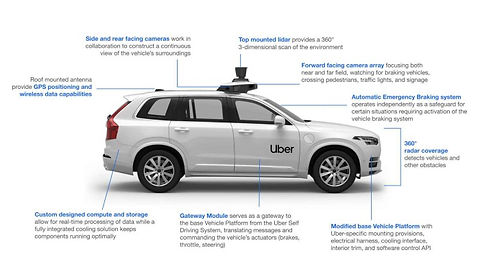

Uber ATG | Test Directorate
Increase Throughput to Autonomy Software
Uber's Advanced Technology Group (ATG) had a large Test Directorate with three senior managers. The group was already pivoting to more simulation for Test.
But our Test Track was a limited resource, COVID-19 was impacting our ability to work in proximity, our organizations ​had evolved without a plan, and we weren't aligned to the new Systems Engineering Directorate.
​
The assignment was to take over as the Director of Test, identify every waste, bottleneck, and opportunity possible, and get 10X the capacity out of Test within months.
​
​
Uber ATG | Mcity IP Negotiation
Securing New Tech to Increase Development Velocity
Real-world engineering development and testing turnaround times were too slow. Our track was our most precious resource, and it was bottlenecking Autonomy's ability to get timely feedback.
​
University of Michigan's "Mcity" had developed software that could help Uber ATG make leap-frog forward, combining our large track and automation with Mcity's track control and routing software.
​
Others before me had identified Mcity as a potential opportunity, but it had fallen off the hardware initiatives list.
​
The challenge was to renew the team's passion for this project, engage with Mcity leadership, and negotiate an IP agreement that would be a long-term win-win for the university and ATG.
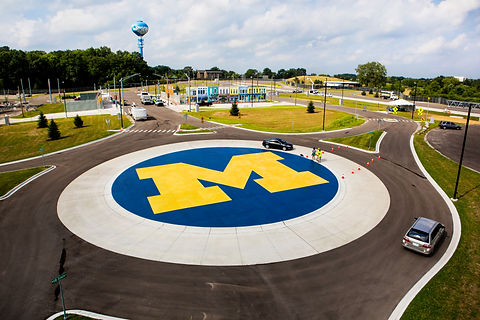
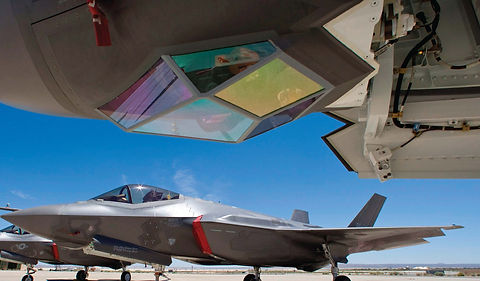
F35 | EODAS
A Study in Engineering Change Management
The Electro-Optical Distributed Aperture System (EODAS) was hands-down one of the coolest technologies in our arsenal. Our cryo-cooled Infrared cameras would feed fighter pilots real-time views from 360 degrees around the F35 Fighter Jet to the Pilot's helmet "Heads Up Display".
​
For over three years, the program had been plagued with engineering, production and reliability problems that would come and go, defying all attempts to stabilize the program.
​
Corporate singled me out to run a full Failure Investigation as a Six Sigma Black Belt and run down all Root Causes of Variation and stabilize the program.
International Space Station (ISS)
C2V2 Program Recovery
(Shown: ISS with Visiting Vehicle)
​
L3 Communications won the $24M Combined Communications for Visiting Vehicles (C2V2) contract in 2012.
It would provide video and audio communications systems for both the ISS and vehicles docking there. Several years later, the program was in real trouble.
Multiple design engineers had left the company, several conflicting design paradigms had been applied simultaneously, and the program was on path to fail.
​
The assignment was to jump in, reverse engineer and understand what had been done, and salvage the program.

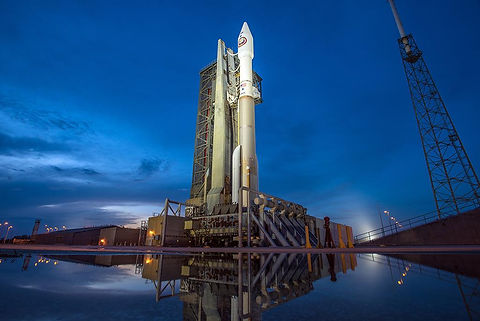
ULA | Atlas V & Delta IV
Combined Control Unit (CCU) Test System
After participating on the technical proposals for the Combined Control Unit (CCU), and then troubleshooting CCU's and other Atlas/Delta avionics, ULA funded additional 7-bay test racks built to increase production rates to support a faster launch cadence.
​
The challenges were legion. Most of the IP walked out the door in a few engineer's heads, right after a Test Engineer exodus. Documentation was either non-existent, or in conflict with itself or the prior hardware builds. Verification methods were not defined. Each existing test stand was a unicorn.
The assignment was to take over as Project Manager, build and train a new team, reverse engineer an operational stand to make proper documentation, develop documented verification methods, and complete the new build.
ULA | Virtual Vertical Integration
Bringing L3Â & ULA Into Partnership
ULA was having an increasingly difficult time competing with the upcoming SpaceX launch vehicles.
​
This assignment was to build a joint approach between ULA and L3 that would provide a technically sound basis for reducing costs to 50% of our baseline, while retaining the safety and performance of the long-standing Atlas V and Delta IV rockets, and winning more content on the new Vulcan rocket.
By the time the project was complete, ULA and L3Harris signed a $1B deal based in part on Tim's foundational strategy, Virtual Vertical Integration (VVI).
​
This approach became part of the Phase Zero briefings to all L3 divisions for the following year.
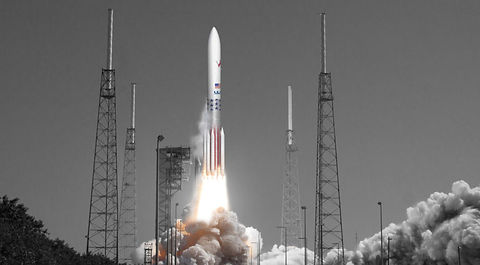

ULA | Avionics Systems
End-to-End Electrical Parts Flow
United Launch Alliance (ULA) was beyond frustrated... they were threatening to change vendors. We kept failing final testing for our Avionics systems due to incorrect parts placed on boards.
In spite of extra diligence throughout the process, better work instructions and design aids, and more Quality Control measures, we continued to find wrong components at the worst possible time, and it was killing both customer confidence in our processes and our schedule commitments.
​
The assignment was to evaluate all the potential Engineering and Manufacturing influences, eliminate the errors, and salvage our customer's confidence.
​
Through working closely with our customer and leaving no stone unturned, we identified 96 possible root causes, and one way to beat them all.
NASA | Space Shuttle
APU Test Cells - Complete Redesign
After decades of wear and tear, the Space Shuttle Auxiliary Power Unit (APU) Test Cells were in dire straits. Archaic test equipment, chart recorders, holding relays, and command and control had to be replaced.
​
The assignment was to rebuild and modernize the APU test cells from the ground up.
​
As the lead engineer for the entire system upgrade, there was a lot to do to meet NASA's standards for Manned Space Flight. Hydrazine protection, modern Data Acquisition, Command & Control, Data Analysis and Reporting, Safety Monitoring, Fire Suppression, and more.
​
See many images and read more on why NASA said we "set a new standard" for NASA test cells.

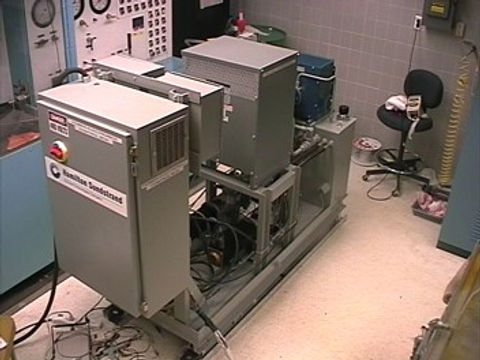
NASA | Space Shuttle EHCE Prototype
Electro-Hydraulic Concept Evaluation (EHCE) - Electric APU NASA Prototype
(Shown: Hydraulic Cart with Pumps, Motors, and Load)
​
NASA wanted hydrazine, a dangerous and explosive chemical used to generate hydraulic power for steering the rocket nozzles, off the Space Shuttle. But was it feasible?
​
The official assignment was for myself and one mechanical engineer to build a simple all-electric dual hydraulic control (DHC) version of the Auxiliary Power Unit (APU). The unofficial assignment was to knock the socks off NASA and win the follow-on.
This downscaled prototype was required to operate two high energy BPM motors and two variable wobbler angle pumps so that NASA could spend the next three years learning. They wanted to experiment with different control algorithms in a live hydraulic system.
After delivery, they knew everything they needed to know in three months.
NASA | Space Shuttle Upgrades
Electric APU Full Scale System
(Shown: Three channel Electric APU, Hydraulic Manifold, and Load System)
​
Following the success of our Dual Hydraulic Control (DHC) prototype, NASA provided us with a 10x funding increase to build a full scale, triple redundant, Electric Auxiliary Power Unit (EAPU). This system could move 90 gallons of hydraulic fluid a minute at 3000 PSI, or about 3 KW of power, enough to replace Hydrazine APU operations on the Space Shuttle.
​
Click below to see how the EAPU became a formal product under the NASA "Space Shuttle Safety Upgrades".
Instead of using LabVIEW and custom PID controls, this time we used Honeywell PID control systems and much larger BPM Motors and larger variable displacement pumps, all feeding into a central hydraulic manifold. We also created a dynamic load. Controlled by joystick, NASA engineers could move the Thrust Vector Control of a nozzle in real-time using the EAPU.
​
After delivery, Brad Irlbeck, the Chief Space Shuttle Upgrades officer, knew we could run the Shuttle off of the EAPU. Now we just had to get the batteries to match!
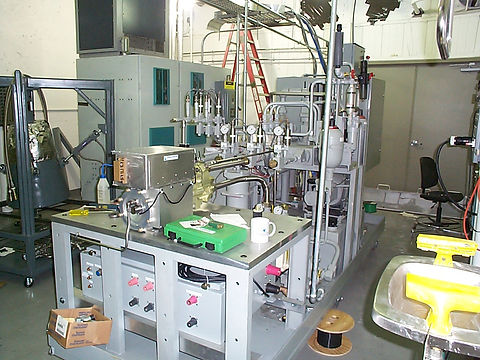

L3Harris | Space Products
Oven Management System
In the rocketry business, processes and process documentation are your lifeblood. If you can't prove a piece was built correctly through your documentation, you may very well scrub a launch!
​
Ovens are used extensively in the manufacture of flight avionics to remove moisture, set ink, cure adhesives, dry conformal coating, and more. Many hundreds of circuit boards move through dozens of ovens across multiple fabrication labs a day. Every time a board is under or over baked, it can invalidate the process, cause tens or hundreds of thousands of dollars in scrap, and create delays for our customers' launches. In our business, a mistake can cost 6-12 months delay to acquire, up-screen, and rebuild parts!
​
The assignment was to create a system that would remove frequent human error from this very manual process in an otherwise manual fabrication lab, and improve flow.
L3Harris | Space Products
Ares I Rocket Avionics Technical Proposal
The end of the Space Shuttle era brought about new proposed rockets for Manned Space Flight. L3 was going all out to bid on the Ares I rocket, which would eventually morph into the current program of record, the Space Launch System (SLS).
​
L3 needed a Systems Engineering based technical strategy that would put us far ahead of the competition on cost for the entire avionics suite, sans the Flight Computer.
​
The assignment was to come up with a technical approach for the design that credibly removed cost across a suite of avionics, build a Technical Proposal volume that sold the approach, and then defend the proposed approach.
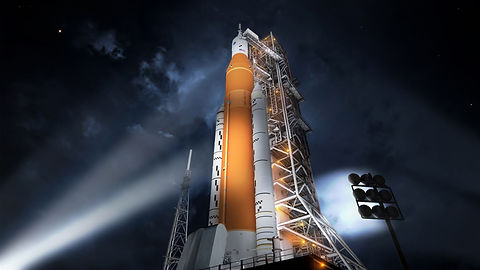

L3Harris | Space Products
Photograph Evidence Stand & Mosaic Analysis
Photographic evidence in the Space Products business is like gold. So valuable in so many ways!
​
When United Launch Alliance needed to know, to see what was inside a unit that had already been built up, tested, shipped, and installed in a rocket ready to launch, there was no substitute for clear high-resolution images of the electronic circuit boards in each phase of buildup. But many of our images were blurred, inconsistent, and it could be difficult to know which of many identical circuit boards a specific image referenced.
​
When we did find something, the question would arise, "But what about all the other boards you built? Prove to me those don't have the same flaw."
​
The assignment was to build a robust system that could answer ULA's questions with confidence every time, and clear products for launch weeks or even months faster.
EVEN MORE PROJECTS!
Click this link to review older or smaller projects that I have worked - in summary format - that contributed to my background knowledge and systems capabilities.
​
Or scroll down to go to the next section.
Project DescriptionThis is your Project Description. It’s a great place to describe your Project in more detail. Add images and provide visitors with essential information about your work, including the project length, partnerships or any successful outcomes. To hook new potential clients, show how your work has provided solutions for past clients.
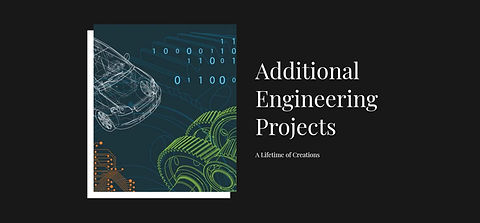
