
F35 | EODAS
A Study in Engineering Change Management
The Electro-Optical Distributed Aperture System (EODAS) was hands-down one of the coolest technologies in our arsenal. Our cryo-cooled Infrared cameras would feed fighter pilots real-time views from 360 degrees around the F35 Fighter Jet to the Pilot's helmet "Heads Up Display".
​
For over three years, the program had been plagued with engineering, production and reliability problems that would come and go, defying all attempts to stabilize the program.
​
Corporate assigned me to run a full Failure Investigation as a Six Sigma Black Belt and run down all Root Causes of Variation and stabilize the program.

The EODAS program allows pilots to see enemies in a 360 sphere all around their F35. They literally can look in any direction, through the fuselage, and see where threats are located using their sophisticated Heads Up Display (HUD) in their helmet.
​
To make this possible, my company created the 6 Cryo-Cooled Infrared (IR) cameras used to stitch together this spherical view. This wasn't just any program for L3 Cincinnati Electronics... This was a massive program that provided the organization's financial base for the IR Products division.
​
We were required to:
​
Keep the IR sensor cool enough to have proper sensitivity
Cool down fast enough to allow pilots to take off quickly
Maintain the reliability
Produce enough cryocooled cameras to meet the fleet's needs
​
We had a good base product.
But most of the units wouldn't cool down fast enough until they had been rebuilt many times, our reliability was not where it needed to be, and as a result, we were continually struggling to get enough product to our customer to meet contractual obligations.
​
After three years of cycling through shotgun fixes only to see the problems recur, our Sector President, Wes Motooka, had had enough. He wanted a Six Sigma Black Belt from Engineering to dig deep and methodically solve this problem.
I was that Black Belt. What follows is a description of my findings, where I will give you an understanding of the depth and breadth of my investigation, while carefully avoiding providing any technical details. In the end, most of this project was about identifying and eliminating sources of variation.
Testing Inconsistently
We had two facilities in the production process, one in California, and one in Ohio. The equipment used to perform testing at each site was different, so bad devices weren't identified at the earliest opportunity and stop shipping parts back and forth.
We had to standardize our test measurements.
Bad Materials
Some of the materials were known to be problematic at high operating temperatures. While a few of the original designers knew this was the best we could find, the risks weren't formally tracked, and there were no ongoing efforts to replace them.
We had to track technical risks formally and transparently.
No Change Control Board
Design and process changes were made at each site without understanding the impacts on each other, or the full design. One hand was always being surprised by the other.
We had to establish a cross-site Change Control Board (CCB) capable of maintaining the configuration and reviewing potential impacts.
Magnets "Upgraded" Without Analysis
Upgrading to stronger neodymium-iron-boron magnets in the compressor could have been a good thing. But without a full analysis of the downstream impacts and necessary controller signal adjustments, it was just bad.
We had to improve our impact analysis before applying changes.
Manual Assembly Process Person Dependent
Months would go by with good coolers, and then a rash of bad ones would infect the line. What changed? The person doing the work. But correlation wouldn't be seen because of the delay from build to integration.
We had to track who did what, and standardize on best practices.
No Detailed Work Instructions
The small shop in California had been purchased because they built excellent cryocoolers at low volume. But their hands-on craftsmanship approach couldn't scale to many products at high volume.
We needed to document a repeatable process more people could succeed with.
Documentation Destroyed
Understanding the history of builds is key to making course corrections. While failed builds and integrations properly went back back to earlier steps, the documentation was frequently started over.
We needed solid process data so we could address the real problems.
Wear-In Components Mismatched
Parts needed to "wear" awhile after assembly. But the pieces used to create fit were disassembled and transported, and weren't being assembled as a set in the final product.
​
We had to control our configuration as matched sets.
Compressor Coils Mismatched
Compressor coils work like speakers, with an electric magnet working against a permanent one. With two coils to a compressor, they needed to be matched so they worked in balance, but sometimes they would use the "leftovers".
​
We had to stop using mismatched coils and stabilize performance.
Improper Tooling on Factory Floor
Assembly tools meant to assist in the placing magnets, coils, and pistons had proven flawed. But instead of removing them from the manufacturing floor, they were left where less experienced fabricators might give them a try.
​
We had to take all inappropriate tooling off the manufacturing floor.
Key Features Not Measured
In cryocoolers, it's all about details. The displacer, where the cooling effect is generated. The gas motions. But we didn't know how many screens to place inside a displacer, and we didn't measure the compressor's ability to move gasses.
​
We had to characterize all items Critical To Quality (CTQ) before final assembly.
Tolerance Stack-Up
Many pieces must line up perfectly for cryocoolers to be efficient. Shafts and pistons in the cold-finger - and in the compressor - had enough play that reassembling the same pieces could give different operational results.
​
We had to review both the mechanical designs and the assembly processes.
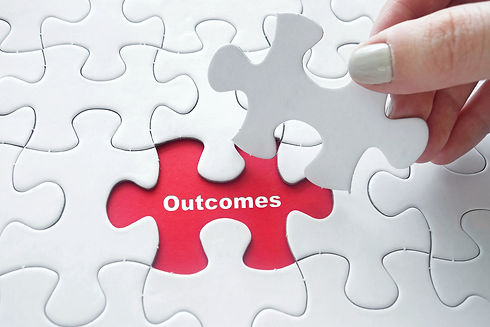
Outcomes
The results of my investigation were extensive, with many topics not included here. The lengthy report included scores of photographs, findings, and detailed recommendations.
Following my report, I briefed every level of management across every related discipline, and launched team after team to resolve the findings. Eventually I moved on to another role, but over the course of three years, others continued my work.
​
Testing was standardized
Critical features were measured before assembly & integration
Manufacturing was centralized and led by new process leaders
Formal processes were created and followed (Travelers and Work Instructions)
Designs & Documentation became managed by a Change Control Board
ALL process documentation was maintained and evaluated.
5S practices were instantiated on the new manufacturing line
​
In fact, my report was still being used as a reference as I was departing L3Harris - providing guidance as they centralized all cryocooler manufacturing to Ohio.
​