
L3Harris | Space Products
Oven Management System
In the rocketry business, processes and process documentation are your lifeblood. If you can't prove a piece was built correctly through your documentation, you may very well scrub a launch!
​
Ovens are used extensively in the manufacture of flight avionics to remove moisture, set ink, cure adhesives, dry conformal coating, and more. Many hundreds of circuit boards move through dozens of ovens across multiple fabrication labs a day. Every time a board is under or over baked, it can invalidate the process, cause tens or hundreds of thousands of dollars in scrap, and create delays for our customers' launches. In our business, a mistake can cost 6-12 months delay to acquire, upscreen, and rebuild parts!
​
The assignment was to create a system that would remove frequent human error from this very manual process in an otherwise manual fabrication lab, and improve flow.

Human error. At the heart of this matter were multiple families of human error that kept plaguing the Space Products group.
​
Second, complexity.
And finally, throughput.
​
In these labs, we built high-mix, low-volume custom made space-grade components.
​
With 10 to 12 Ovens and Thermal Chambers per lab, and each oven at different set temperatures, and from 12-40 pieces in any oven at any given time, and each piece needing to be baked as a specific temperature for a specific duration based on the specific process (dry-out, ink cure, paint cure, conformal coating cure, epoxy cure, etc.)
​
At any given time, it is very difficult to remember what was where, and for how long! To boot, many of the boards and components look similar or identical.
Thousands of parts were correctly processed every year. But it only takes a few errors a month to throw a program into a tailspin! With all of the opportunities for human error, any Poka-Yoke (mistake proofing) effort would require a solution we couldn't find commercially.
​
Parts were being misprocessed by Fabricators by:
Writing times illegibly
Forgetting to document a start or end time when loading or removing parts from an oven
Placing parts in ovens set at an incorrect temperature for the specified process step
Over or under baking parts (which at higher temperatures can ruin parts) by pulling too early or forgetting to pull on-time.
Every time a board was "misprocessed", it created turmoil in the program. Is it safe for flight? Do we have enough parts to build another? How will this look to the customer? How badly impact our schedule? And most importantly, HOW do we stop this from happening?
​
I proposed a solution to the Director of Manufacturing and one of his senior managers, but I failed to win the day. After another two years of periodic failures and failure review boards (FRB), and a very frustrated customer, I found myself on a Tiger Team on this same issue. "I can fix this." I once again laid out my approach, and this time got the green light.
Incorrect Start/Stop Documentation
Fabricators would occasionally make errors documenting bake times on travelers. Messy writing, transposed numbers, missing dates or times for start or end times, incorrect oven used or recorded, and more. Sometimes operators would write times in temporary locations and then lose them.
​
What was needed was a modern system that could track ALL start/stop times for ALL parts loaded into ALL ovens, that would mistake proof them
Incorrect Part/Process Documentation
Fabricators are working many pieces of many products at once. For Space Products, every single piece has to not only be processed correctly, it has to be documented correctly. If process and documentation don't match, you have SCRAP.
​
What was needed was a system that guided fabricators to selections based on the current step in the manufacturing process, but that didn't require cross-correlation of drawings, work instructions, and travelers.
Wrong Oven Temperature
Placing parts into ovens set at the incorrect temperature is easy to do. They all look similar, and sometimes that same part needs to go into that other oven (for a different process step).
​
What was needed was a way to have the system tell Fabricators which oven to place the part in, without the Fabricator having to cross-correlate process steps, required set-points, and matching ovens.
Simple to Configure Ovens
Ovens were periodically added to or removed from each lab. More frequently, the oven setpoints would be changed to support volumes of parts in production at that time and the required bake space for processes. We needed a simple text-based configuration file that lab managers could update and the ovens would simply "work".
​
What was needed was a system that would allow lab managers to change oven temperature set-points, and the system would dynamically redirect fabricators to the correct ovens with the new settings to match part bake requirements.
Simple to Configure Product Parameters
New products, parts and changing manufacturing processes were always going to be in a state of flux. Any solution would have to be dynamic and flexible without requiring the system to be modified or recompiled.
​
What was needed was a simple to use text-based configuration file that lab managers could create and update from templates without any outside support. Create a new file, and the options dynamically show up in the system!
Fabricator Friendly
Our fabricators had not been required to use PC's to accomplish their work, and as a result, we had a wide range of PC literacy in the lab. If the system was complicated or difficult to use, some experienced fabricators would struggle to use it. It wouldn't gain full adoption, and we wouldn't see the benefits.
​
What was required was a Graphical User Interface (GUI) that would be easier to use than their current paper-based processes.
Stop Overloading Ovens
Ovens were often overflowing with parts, even as other ovens set at the same temperature were under-utilized.
​
What was needed was a way for the Fabricator to see how full each appropriate oven was before selecting it.
WIP Sitting in Ovens
Sometimes work in progress (WIP) is O.K. to stay longer, even overnight. But when parts become forgotten or ignored, it creates a situation where new parts cannot be loaded because only one person knows when the old parts can come out.
WIP that isn't moving also created delays in the manufacturing processes depending upon those parts!
​
What was needed was a way to make everyone aware who had placed what into each oven, and when those parts should be removed, to keep processes moving and capacity available.
Audit Trail of Properly Completed Bakes
Whenever there was a question by management or our customers, it was very difficult to reconstruct why errors happened. There was always some level of a shared acceptance of risk anytime we moved forward with parts that may not have been properly processed. Our customers really didn't like that!
​
What was needed was a system that kept historical records of every part in every oven over time, creating a full audit trail.
Power Failure Safe Recordings
Ovens drew too much current for them to be on the power backup system, and were therefore vulnerable to utility company power outages. But how long were the items baked before the outage? How much to go?
What was needed was a minute-by-minute recording that knew when any oven temperature dropped below requirements, stopping the individual timers for every part, and continued the timers when power was restored and temperature recovered.
Automated Labels for Parts & Travelers
Putting parts into the correct oven was a good start, but with so many parts looking similar or identical, how can we be sure the Fabricators will pull the correct part with the correct serial number?
​
What was needed was a thermally safe label printer that would generate labels to sit with the part in the oven, and another label at bake completion to paste onto the Traveler documentation.
Alarm Limit Monitoring
Previously every oven required its own Over/Under protection hardware, redundant to the oven's own temperature regulation hardware. These devices would sound if a limit exceeded some margin beyond normal controls.
​
What was needed was a single system that could monitor the status of all ovens in a lab, and create alarms, warnings, and emails if there was a problem. We needed to get out of calibrating so many tools and create real notifications.
Oven Management System Gallery
Click images to enlarge and make text easier to read
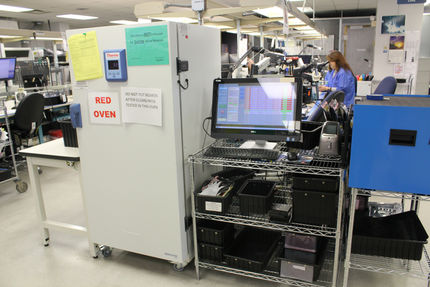